Insights
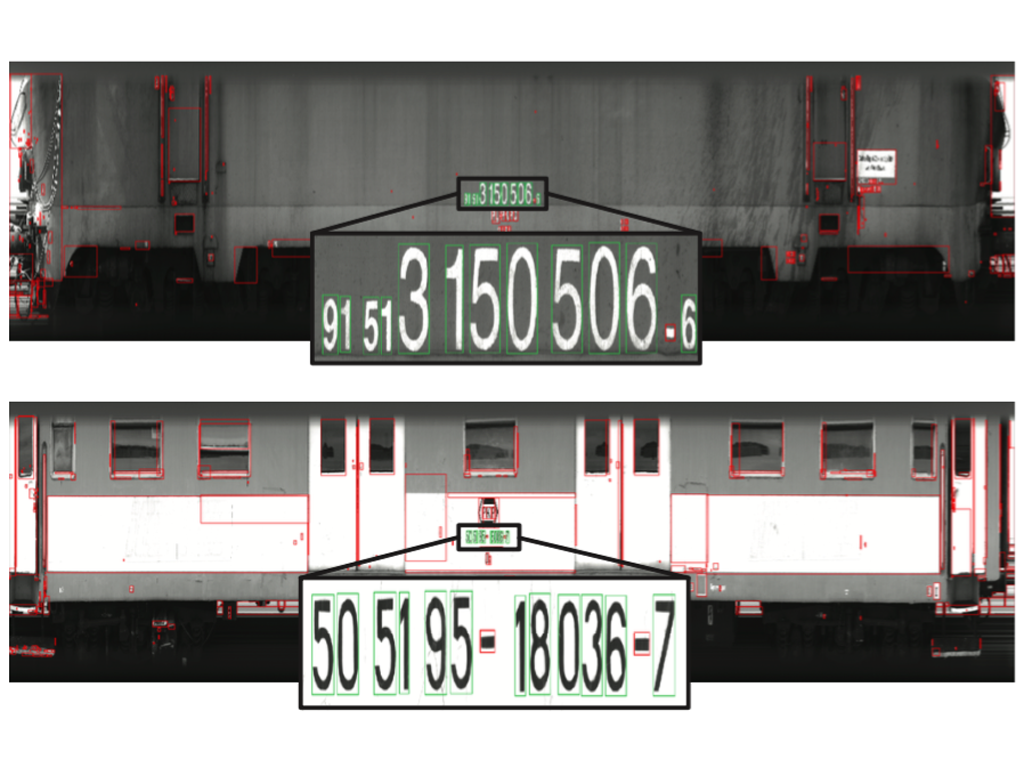
We designed a machine vision system to efficiently monitor, analyze and present visual data acquired with a railway overhead gantry equipped with multiple cameras. This solution aims to improve the safety of daily life railway transportation in a two-fold manner: (1) by providing automatic algorithms that can process large imagery of trains (2) by helping train operators to keep attention on any possible malfunction. The system is designed with the latest cutting edge, high-rate visible and thermal cameras that observe a train passing under an railway overhead gantry. The machine vision system is composed of three principal modules: (1) an automatic wagon identification system, recognizing the wagon ID according to the UIC classification of railway coaches; (2) a temperature monitoring system; (3) a system for the detection, localization and visualization of the pantograph of the train.
These three machine vision modules process batch trains sequences and their resulting analysis are presented to an operator using a multitouch user interface.
Two linear cameras (4096×1 pixels @ 18500Hz) are used to observe the profile of train and stitch a complete image of the train seen laterally. These images can then be used to extract the identifier of each wagon and to detect the train pantograph in order to avoid false-alarm in the shape analysis sub-system. Finally, two thermal cameras (256×1 pixels @512Hz) are used to segment train temperature and compute maximum and average temperature over a grid of sub-regions.